Avant Propos :
Les systèmes de productions font l’objet d’études lors de leur conception. Ils sont dimensionnés et calibrés par rapport aux besoins connus alors.
Les plans de production sont dictés par les besoins clients qui peuvent être très volatile. Il faut donc sans cesse s’adapter : un vrai casse-tête pour l’organisation de la production.
Nos clients nous demandent de plus en plus l’utilisation de nos modèles de simulation pour les aider dans la validation de l’ordonnancement de leur production.
Nous vous proposons ici l’exemple de l’utilisation d’un modèle de simulation sous le logiciel AutoMod depuis la phase de dimensionnement jusqu’à la phase d’optimisation de la production.
Sommaire :
- Contexte et Objectif
- Présentation du process
- Simulation
- Étalonnage et Analyse
- Expérimentation
- Résultats
- Conclusions
Contexte et Objectif :
Le site nucléaire du Tricastin est un site industriel qui regroupe des installations du cycle du combustible nucléaire et une centrale nucléaire. Il est situé en France, dans la basse vallée du Rhône, au cœur de la région historique du Tricastin.
Le site accueille la plus importante concentration d’industries nucléaires et chimiques de France. C’est le site nucléaire le plus étendu de France devant l’usine de retraitement de La Hague. Le site regroupe de nombreuses activités liées à la fabrication et l’exploitation du combustible nucléaire.
Six entreprises interviennent sur le site Orano (auparavant « Areva », jusqu’en 2018).
La Société d’Enrichissement du Tricastin (SET) exploite l’usine d’enrichissement d’uranium par centrifugation Georges-Besse II, qui remplace depuis 2012 l’ancienne usine Georges-Besse.
Cette usine est constituée de deux unités, Sud et Nord, séparées physiquement sur le site, qui ont été mises en service progressivement, grâce à leur conception modulaire.
En juin 2012, la nouvelle usine atteint une production suffisante pour permettre le passage de relais avec l’usine Eurodif/Georges-Besse. L’ancienne usine (Georges-Besse I) est donc fermée. Son démantèlement s’étendra sur une quinzaine d’années.
En 2016, Georges-Besse II atteint sa pleine capacité, avec 7,5 MUTS (millions d’UTS).
SET a demandé à SIMCORE la modélisation des différentes usines (GB2N, GB2S, REC2) ainsi que les parcs de stockage pour dimensionner et valider :
- Les hypothèses techniques de fonctionnement
- La capacité des manutentions (Pont roulants, chariots)
- La capacité des équipements spécialisés,
- Le stockage (en respectant des contraintes de zonage…)
Et ceci en fonction d’objectifs de production et de contraintes liés aux produits.
Le projet a débuté en 2007 et des mises à jour sont toujours effectuées (les dernières en 2019).
Présentation du process :
L’usine Georges Besse II (GB II) est une usine d’enrichissement isotopique de l’uranium par ultracentrifugation.
L’usine GB II est composée de deux unités (nord et sud) d’enrichissement, et d’un atelier support, le REC II. Cet atelier est destiné notamment à assurer les fonctions de transfert, d’échantillonnage et de contrôle de la matière.
L’activité principale est la transformation de l’UF4 en UF6 et l’enrichissement nucléaire.
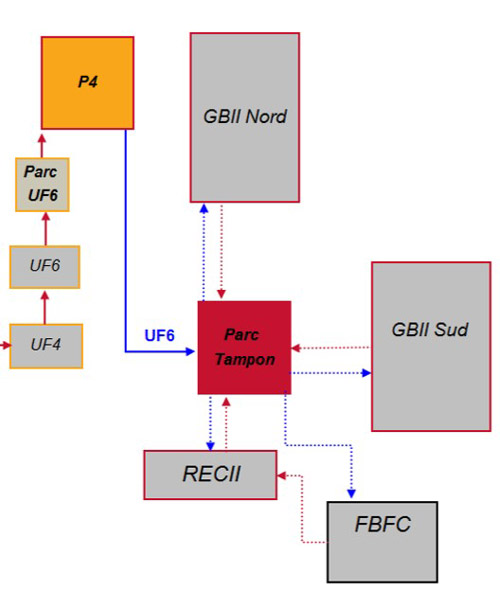
Simulation :
Modélisation sous AUTOMOD :
Le modèle de simulation est modulaire, chaque usine peut fonctionner indépendamment. Ceci a permis de travailler sur les études au fur et à mesure de la création des entités.
Chaque usine est simulée en détails. Les moyens de manutentions utilisent les circuits réels, les vitesses de déplacements définis par l’exploitant et les règles de circulations conforment aux normes de sécurités.
Les temps procédés sont définis de façon enveloppe pour des contraintes de confidentialités.
Les temps de process étant relativement long, la simulation traite jusqu’à 3 ans de production (en quelques minutes !!).
La simulation permet de tester des projections de planning de production pour remonter à la direction des ventes les capacités disponibles par type de produits.
Étalonnage et Analyse :
Lors de la phase de mise en service, le modèle de Simulation a été adapté pour correspondre au fonctionnement du système réel.
Cela a notamment permis de proposer des optimisations sur les règles de fonctionnement des ponts roulants qui ont une faible utilisation mais un besoin de forte réactivité.
Durant les plus de 10 ans de maintien du modèle, après chaque évolution, des tests de non régressions ont permis de s’assurer de la continuité de la qualité des résultats fournis.
Expérimentation :
Les différents modèles ont 3 phases d’utilisation :
- En phase d’étude :
- Avant la construction afin de confirmer le dimensionnement des installations.
- En phase de réalisation :
- Mettre à jour la simulation en fonctions des évolutions dû à la réalisation et de mesurer les impacts pour ajuster les besoins.
- En phase de production :
- Tester des modes de fonctionnements différents,
- Introduire de nouveau plan de production et trouver les meilleurs ordonnancements pour le lancement des productions.
- En cas de nouvelle commande urgente, tester des ordonnancements différents avant les lancements.
Scénario Changement de plan de production : Tous les mois lorsque la direction des ventes redescend les besoins de production, il faut ajuster l’ordonnancement de la production. La simulation permet de tester les différentes propositions faites par les experts.
La gestion des stocks et des dates de livraisons sont les objectifs principaux.
Scénario Amélioration continue : Le service de gestion des procédés utilise les données réelles pour analyser le fonctionnement. Les systèmes demandent des ajustements réguliers des consignes de production ce qui modifie les temps de production.
En cas de variation importante il est nécessaire de vérifier les occupations des zones de stockage pour lancer des mouvements pour libérer de la place ou au contraire accélérer les approvisionnements. Les temps de manutentions étant long il faut anticiper de plusieurs jours.
Les différents runs de simulation sont exécutés. A la fin de chaque runs les résultats sont importés dans un fichier Excel afin de l’analyser.
Résultats :
Les résultats fournis par la simulation sont les suivants :
- Utilisation des ressources
- Nombre de déplacement, % d’Utilisation, Dépose, Prise, Replis, % Libre pour les transbordeurs et les chariots E/S,
- Nombre de conteneurs, % d’Utilisation, Réserve, Attente cycle, Cycle, Attente Station, Attente Manut et % Vide pour chaque poste de travail.
- Récapitulatif du nombre de gammes effectuées
- Résultats sur les commandes (Date de mise à disposition)
- Synthèse des taux d’utilisation des ressources :
- Transbordeurs
- Chariots E/S
- Lignes de production
- Tous les équipements
- Graphiques à abscisses paramétrables permettant d’analyser :
- Gammes en cours et en attente
- Utilisation temporelle des moyens de manutention
- Consommation électrique.
- Listing de l’enchainement des opérations dans l’atelier issu des fichiers générés par le modèle AutoMod.
- Résultats parc tampon :
- Flux de conteneurs total annuel sur le parc,
- Nombre et durée de chargement / déchargement de wagons,
- En-cours de conteneurs instantané et moyen sur le parc.
Conclusions :
Les conclusions du responsable Procédé SET sont les suivantes :
- Le modèle de simulation donne des résultats d’une grande précision, ce qui permet de comparer les scénarii et communiquer des informations fiables au décideurs,
- Permet une meilleure compréhension et implication de tous les acteurs internes et externes,
- Un outil idéal pour :
- La Planification (plan de charge, plan de production),
- Étudier les extensions,
- Formation,
- Valider les bons dimensionnements des parcs de stockages (volume et zonage),
- Définir
Cela permet également d’avoir une vision sur l’avenir en anticipant les investissements pour des équipements qui deviennent goulot.
Dans les évolutions envisagées :
- La possibilité d’utiliser la simulation pour des démarrage à chaud (tenant compte de l’état courant de l’installation venant des outils opérationnels)
- Inclure les plans de maintenance,
- Aller plus loin dans la partie ordonnancement grâce notamment au démarrage à chaud.