Avant Propos :
Dans l’industrie il faut régulièrement réaménager son atelier ou ses lignes de productions pour des changements de machines, inclure de nouveaux produits ou optimiser la circulation des produits et des moyens de manutention.
Plusieurs approches sont possible, nous vous proposons ici l’exemple de l’utilisation d’un modèle de simulation sous le logiciel Simul8.
Cette approche permet :
- De trouver le bon emplacement des machines,
- Évaluer l’état de congestion des différentes zones de circulation,
- Dimensionner ses stocks (principaux et tampons),
- …
Pourquoi Utiliser la Simulation de Flux pour son implantation d’atelier?
On peut faire un parallèle entre la CAO versus la planche à dessin.
La création d’un modèle de simulation prend plus de temps que le simple dessin sur une feuille papier. Cela nécessite également un logiciel spécialisé.
Simcore est là pour vous accompagner soit par de la formation soit par de la prestation de service.
Car une fois la base du modèle de simulation réalisé tout devient plus rapide. Il est alors possible rapidement de :
- Modifier et déplacer les équipements (machines, manutention,…),
- Modifier et déplacer les stocks,
- Changer les zones et chemins de circulation,
- Évaluer avec des programmes de production différents (volumes, typologie…)
- Évaluer des ordonnancements différents
Contrairement à un simple dessin, la simulation vous donnera des résultats visuels et chiffrés et ceci en quelques minutes.
Nous vous proposons d’illustrer nos propos avec l’exemple d’une étude pour une usine de production de canettes métallique sous le logiciel SIMUL8.
Sommaire :
- Contexte et Objectif
- Présentation du process
- Simulation
- Étalonnage et Analyse
- Expérimentation
- Conclusions
Contexte et Objectif :
Spécialisée dans la transformation de bobine d’aluminium en boîtes de boisson, un atelier de l’usine de ce client doit être réorganisée pour répondre à plusieurs besoins :
- Établissement d’une cartographie du fréquentiel des flux (bobines, viroles, déchets, …),
- Réduire les risques pour les opérateurs lors des opérations de manutention et pour cela identifier les carrefours à risques,
- Analyser les évolutions des stocks (pannes, température, …),
- Modélisation et étude d’impact de nouvelles solutions pour la manutention des différents produits,
- Identifier les problèmes de capacité éventuels (machines, stocks, ressources, …)
Présentation du process :
Type de flux étudiés :
- Bobines, viroles et déchets.
- Modélisation de 80% des références (non prise en compte des références à faible volume)
Moyens de manutentions :
- 3 caristes 17T
- 1 cariste 7T,
Les contraintes de flux modélisées sont :
- Les temps de cycle et les pannes machines,
- Les ressources pour la manutention des produits,
En prenant l’hypothèse que les données fournies par le client (temps de cycle et lois de pannes) sont correctes, la précision des résultats fournis par le modèle est de l’ordre de 5% (calibrage).
Simulation :
Modélisation sous Simul8:
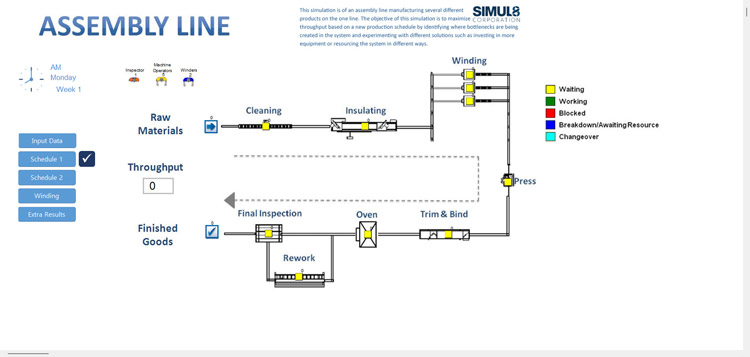
Le premier objectif étant la réalisation d’un fréquentiel des flux, chaque zone de l’atelier a été représenté ainsi que la représentation du schéma de circulation.
Ainsi chaque chemin origine/destination est modélisé. En fonction de la fréquence horaire dans chaque zone, les couleurs sont mises à jour conformément à l’échelle (Fréquence moyenne de passage horaire). On obtient alors 2 types d’informations :
- Une information visuelle, qui permet de voir l’évolution tout au long de la période simulée,
- Une information chiffrée, avec l’analyse statistique de ce fréquentiel.
Étalonnage et Analyse :
Durant la phase de calibrage, on compare (lorsque cela est possible) des points de mesures du modèle de simulation avec le système réel.
Les écarts sont alors analysés et corrigés si nécessaire. On parle du scénario 0 qui correspond à la situation actuelle de l’installation.
Par la suite on ne fera des comparaison qu’entre modèle de simulation.
Expérimentation :
Une fois le modèle de simulation réalisé et calibré, il faut maintenant l’exploiter.
Pour cela on va lancer des « runs » qui sont l’exécution de la simulation en fonction:
- d’une configuration du modèle (nombre de machine active, mode de fonctionnement …),
- d’un jeu de données d’entrées (film de production, cadences horaires…),
- de la valeur des paramètres (nombre d’opérateur par zone, temps de cycle des machines, état des stocks …)
Pour comparer les résultats il faut définir des indicateurs. Si possible utiliser ceux qui existe dans le système réel car ils seront mieux compris par les équipes.
Dans cet exemple, on a fait varier :
- les programmes de production,
- Les temps de cycle et les pannes machines,
- Les ressources pour la manutention des produits.
Les indicateurs portaient sur :
- Les fréquences de passage dans les carrefours,
- La production hebdomadaire réalisée,
- Le temps moyen de traversée,
- Les taux d’engagement des ressources.
Étude 1 : Quels sont les carrefours les plus sollicités dans l’atelier?
Analyse des résultats étude 1 :
- On observe un grande dispersion sur les fréquences horaires (de peu de trafic à beaucoup de trafic).
- Les mouvements du tracteur peuvent être divisés par deux dans l’allée principale en modifiant son point d’entrée dans le hall.
- Les carrefours les plus dangereux sont situés dans l’allée principale (Piétons, tracteur, cariste 7 tonnes et 17 tonnes).
- Les flux viroles et bobines représentent environ 80% du total des mouvements (Répartition: 50-50)
Conclusion étude 1 :
Suite à l’étude le plan de circulation a été modifié, notamment pour le tracteur. L’objectif de réduire la fréquence des mouvements horaires en dessous de 20 par zone a pu être atteint.
Une solution d’automatisation de la manutention a été étudiée mais non retenue en raison de l’impact négatif sur la production.
Étude 2 : Quelle évolution du fonctionnement de l’atelier après les modifications préconisés par la simulation?
La méthode utilisée lors de l’étude de simulation est l’analyse des points bouchons et l’adaptation des temps de cycle correspondant.
Par exemple, l’information transmise au client est que pour atteindre sont objectif de production il faudrait accélérer la cadence de production de la machine L8 de 5%.
Le client étudie alors les possibilités technique d’amélioration :
- maintenance préventive,
- optimisation (temps de changement, de réglage,…),
- stock tampon amont pour ne pas désamorcer la machine
- Stock aval pour ne bloquer la machine en cas de saturation aval
- …
Exemple d’analyse des résultats étude 2 :
- Machine 2 : Il faut réaliser 8% de productivité qui peuvent être obtenues en baissant de 10% les temps de cycle ou en faisant passer le taux de pannes de 43% à 35%.
- Machine 3 / Machine 4 : Répartition 2/3 Machine 3 et 1/3 Machine 4 un peu juste car nous devons diminuer de 15% le temps de cycle de la Machine 3 pour passer le volume
- Cariste 7T : Charge Cariste 7T trop élevée mais non pénalisant (les taux de charge usuels ne dépassent pas 80%).
Les focus portés sur les éléments goulots ont permis de mettre les efforts aux bons endroits. Les actions ont conduit à la réduction de 50% du taux d’utilisation du Cariste 7T, ce qui a permis d’améliorer la réactivité et réduire des temps d’attentes.
Grâce aux améliorations le client a pu réduire son temps moyen de traverser de 8.6% et donc améliorer son taux de service (et réduire les coûts liés à l’immobilisation des produits).
Étude 3 : Quel est l’impact d’une panne sur un équipement?
Mise en place d’une panne d’une semaine sur Machine 4 en début de mesure et simulation pendant 8 semaines.
L’objectif est de mettre en panne un équipement pendant une période relativement longue et de mesurer le temps nécessaire pour un retour à la normale.
Si le système ne retrouve pas une position d’équilibre, c’est que l’équipement est critique.
Il est possible d’essayer plusieurs durée pour définir le temps maximum d’arrêt d’un équipement.
Analyse des résultats étude 3 :
Les ‘grosses’ pannes (1 semaine) sont absorbés par les différents stocks qui n’atteignent pas leurs capacités maximales.
Stock A :
- On observe une augmentation progressive du niveau du stock (+ 150 bobines).
- Après la panne, le niveau du stock redevient normal après un peu plus de 2 semaines de production.
Stock B :
- On observe une augmentation progressive du niveau du stock (+ 170 bobines).
- Après la panne, le niveau du stock redevient normal après un peu plus de 2 semaines de production.
Conclusion étude 3 :
Cette étude a permis de vérifier que les stocks étaient suffisamment dimensionnés pour accepter l’augmentation de besoin lié à la panne (avant de bloquer d’autre machines).
On a pu mesurer que le temps de rétablissement était 2 fois la durée de la panne.
Ce genre d’étude a été reproduite sur les différents équipements, cela a notamment permis la création de consignes pour les équipes de maintenances (priorités d’intervention, mis en place de maintenance préventive pour les équipements les plus critiques).
Conclusions des études :
La modélisation d’atelier de production permet d’apporter des réponses à plusieurs services de l’entreprise:
- Gestion des risques liés à la circulation dans les zones de productions et logistiques,
- Optimisation des moyens de production : Répondre à la question comment produire mieux avec nos équipements?
- Préconisation pour la maintenance des équipements (définition des délais d’interventions, des équipements critiques…)
- …
Le retour sur investissement se fera d’autant mieux que les différents acteurs prendront part à l’étude.
Un responsable de l’étude, côté client, doit tout de même veiller à la définition des priorités.