Avant Propos :
Simcore réalise de nombreuses études de dimensionnement pour des ateliers de production. Le contexte est souvent le même, une augmentation de besoin de production et des questionnements sur la capacité de production des équipements. Dans de nombreux cas l’ajout de matériel est pressenti, mais le client sollicite une étude pour confirmations.
Dans 80% des cas une meilleure utilisation des équipements existants, éventuellement l’ajout d’opérateur suffit à couvrir le besoin.
Nous vous proposons un exemple basé sur l’étude de la réduction des temps pour illustrer le propos et répondre à la question : « Pour augmenter la production, faut-il ajouter une nouvelle machine ?
Sommaire :
- Contexte et Objectif
- Présentation du process
- Simulation
- Étalonnage et Analyse
- Expérimentation
- Résultats
- Conclusions
Contexte et Objectif :
Un Atelier produit 8.2 lots par 24h. Un nouveau marché nécessite de passer à 10 lots/24h.
Le client pense qu’il faut ajouter une machine supplémentaire et il souhaite que la simulation l’aide à valider sa décision.
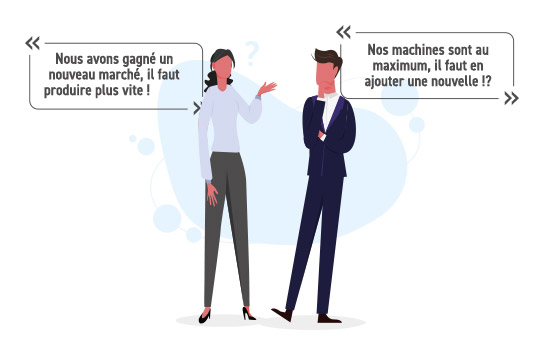
Présentation du process :
1 Atelier séparé en 3 zones (Z1, Z2 et Z3)
L’atelier dispose de 9 lignes de production partageant certains moyens et contraignant leurs voisines en fonction des étapes de leur production.
Chaque process est décomposé en une trentaine d’étape. Chaque étape nécessite des conditions de réalisation avant de passer à la suivante (Disponibilité de ressources, Règles ou condition de démarrage de l’étape valide, Temps de réalisation de l’étape).
Les Ressources principales sont :
- Les opérateurs,
- Les 2 chariots manipulateurs,
- Les moules,
- Les ponts Roulants en Zone 1 ou en Zone 2,
- Un équipement spécifique…
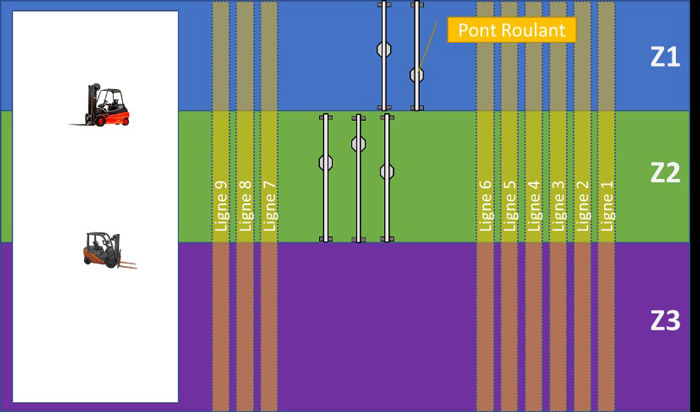
Simulation :
Modélisation sous SIMUL8 :
Étalonnage et Analyse :
Après étalonnage du modèle (8.2 Lots /24h dans la réalité contre 8.16 Lots /24h dans la simulation) et afin de s’assurer de l’intérêt du nouveau moyen une étude d’augmentation de potentiel de production est réalisée en surveillant les causes de non production en sortie d’atelier :
La liste des attentes principales et identifiables est la suivante :
La production de l’atelier est donc de 8.16 lots en 24h.
La recherche de l’optimisation des potentiels de production se fera en essayant l’idée du client d’ajouter le nouveau moyen ou en faisant « sauter » les points bouchons les uns après les autres jusqu’à atteindre l’objectif de 10 Lots par jour.
Expérimentation
Scénario 1 : On compare l’ajout d’une machine et l’ajout de l’élément entraînant le plus d’attente (ici l’opérateur (40% du temps d’attente).
Résultat Scénario 1 : On obtient une meilleure production avec l’ajout de l’opérateur. Cette configuration devient la nouvelle configuration de référence.
L’étude des temps d’attente donne la nouvelle répartition :
Scénario 2 : L’attente Pont_Z2 et l’attente Opérateur sont proche, on compare donc 3 configurations :
- Ajout d’une machine
- Ajout d’un second opérateur
- Ajout d’un pont roulant en Z2
Résultat Scénario 2 : On obtient une meilleure production avec l’ajout de l’opérateur. Cette configuration devient la nouvelle configuration de référence. On n’atteind pas les 10 lots/24h, on cherche encore à augmenter la production.
L’étude des temps d’attente donne la nouvelle répartition :
Scénario 3 : L’attente Pont_Z2 est le poste correspondant à la plus grande perte de production. On compare l’ajout d’une machine et l’ajout d’un Pont Roulant en Z2.
Résultat Scénario 3 : On obtient une meilleure production avec l’ajout du pont roulant. Cette configuration devient la nouvelle configuration de référence. On n’atteind pas les 10 lots/24h, on cherche encore à augmenter la production.
L’étude des temps d’attente donne la nouvelle répartition :
Scénario 4 : L’attente Pont_Z1, l’attente Opérateur et l’attente poste de prépa sont proche, on compare donc 4 configurations :
- Ajout d’une machine
- Ajout d’un nouvel opérateur
- Ajout d’un pont roulant en Z1
- Ajout d’un poste de prépa
Résultat Scénario 4 : On obtient une meilleure production avec l’ajout du poste de prépa. On atteind les 10 lots/24h, on peut donc s’arrêter là.
L’étude des temps d’attente donne la nouvelle répartition :
Résultats
Le client a souhaité ajouter la machine supplémentaire. Nous avons donc refait l’étude en incluant en première étape l’ajout de la machine. On peut comparer les 2 résultats sur le graphique suivant :
Conclusions
Pour obtenir la production souhaité, l’ajout du pont roulant Z2 et le poste de prépa sont obligatoire. Dans le cas de l’ajout de la machine, il faut ajouter un pont roulant en Z1 ; dans l’autre cas 2 opérateurs sont nécessaires.
La question se pose donc sur la durabilité du besoin.
En cas de besoin ponctuel, l’ajout des 2 opérateurs est plus flexible ; dans l’autre cas il faudra s’assurer du ROI par rapport au coût des éléments ajoutés.